The rotary kiln is mainly used for calcining chemical clinker. It is mainly used for roasting various metals and various refractory materials in the metallurgical industry. What effect does its packing density have on the use of equipment? The following article explains in detail for everyone, let's take a look at it together.
1. When the kiln is too dense, it will directly cause a large airflow resistance in the rotary kiln, which is conducive to ventilation and the temperature in the kiln is uneven.
2. The minimum distance between the blank and the blank should be controlled at about 5mm. When loading blanks, the flame is nakedly fired with a slab pillar structure, and each slab is supported by three pillars.
3. Keep the upper and lower sheds flat, stable, straight, and evenly arranged. The products of each layer should be as high as possible and have different shapes and sizes.
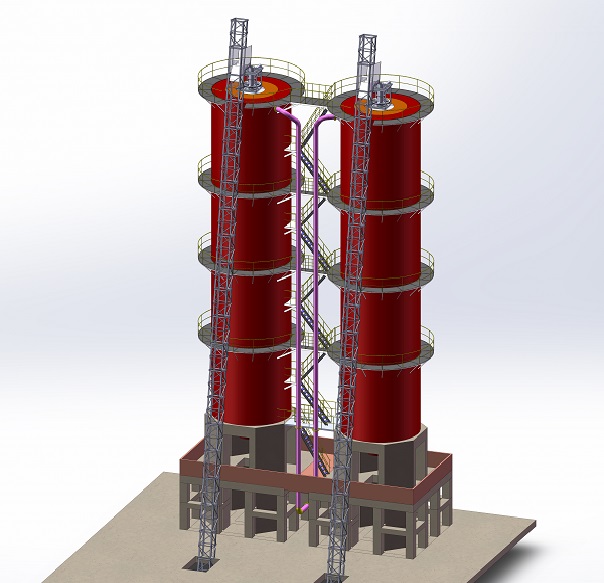
4. The full vehicle loading blank should be installed in the middle position with the shortest blank.
5. The green body is high, and the long column is placed at the uppermost lowermost part, which is conducive to maintaining the thermal balance of the rotary kiln green body under high-temperature airflow, thereby shortening the firing time and reducing fuel consumption.
6. The product blank placed on the shed plate should be properly coded when the blank is loaded, to prevent the air flow being too fast and being pumped away by the chimney, and improve the heat utilization rate.
It is said in the comprehensive article that when using rotary kilns, some measures should be taken to control the density of the kiln, so that the temperature in the equipment can be controlled, so as to maintain heat balance, improve heat utilization, reduce heat loss, and reduce The waste of raw materials.